
#Stock turnover formula how to
How to find finished goods inventory requires three piece of information:Īll three of these are used in the finished goods inventory formula. Whenever anyone speaks about calculating finished goods inventory, they’re talking about ending finished goods inventory. There are two types of finished goods inventories: one at the beginning of an accounting period and one at the end. How to Calculate Finished Goods Inventory
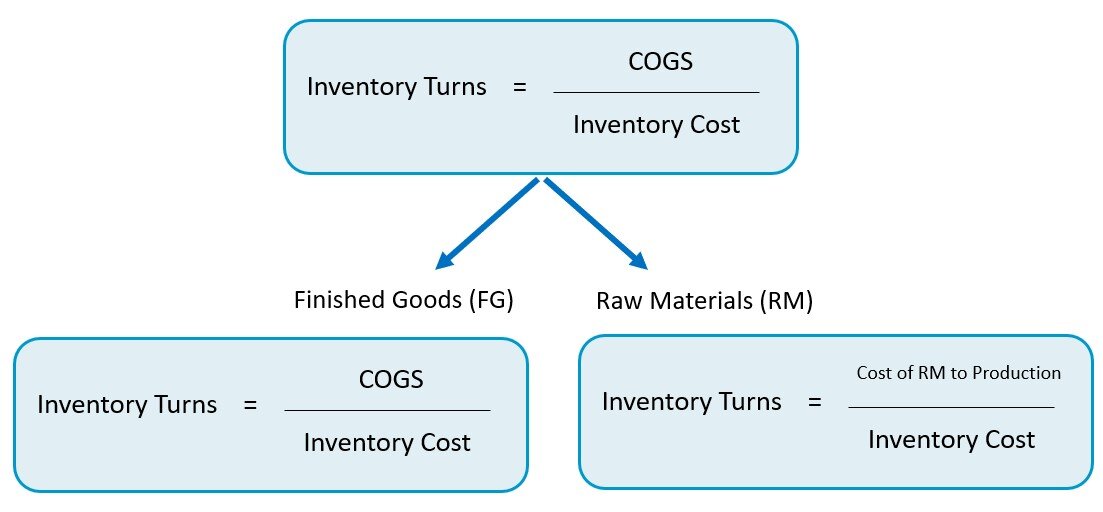
Most of these goods are also assigned a SKU number. Once finished, these goods can ship and it's time to focus on inventory tracking. Finished goods inventory is what manufacturers depend on to generate revenue. When the manufacturing process is finished, the work in process becomes a finished good. In those instances, companies move straight from raw materials inventory to finished goods inventory. There are some very short or simple manufacturing processes that don’t require specific reporting of WIP inventory.

This is when the actual manufacturing is happening.
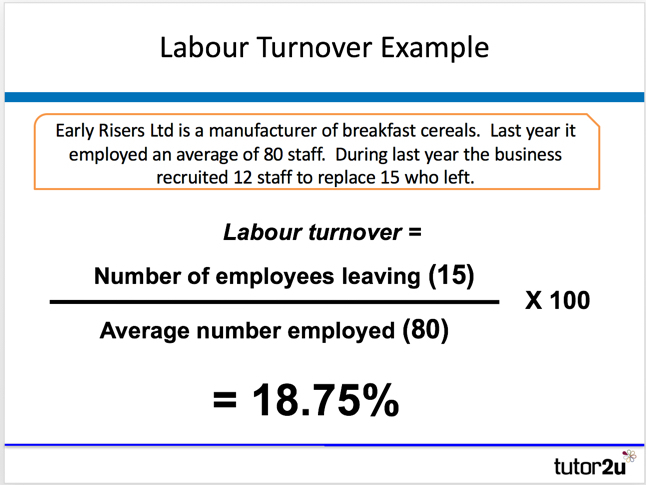
Work in process inventory (AKA work in progress or WIP inventory) is everything that happens to inventory in between raw materials and finished goods. It’s been moved out of its initial warehousing environment and is now a work in procress. At that point, the inventory is no longer raw. They’re considered raw materials inventory until they’re combined with human labor. Raw materials inventory is all the ingredients or base component parts that will be used in the production process. Here’s how it all goes down: Step 1: Raw Materials Inventory There are three main steps involved in transforming raw materials into finished goods inventory. Finished goods inventory becomes finished goods inventory by first being the other two types of manufacturing inventory. To better understand the finished goods produced formula, it's essential to grasp the entire manufacturing process. Becoming Finished Goods Inventory: The Journey from Raw Materials to Finished Goods Inventory The destination of these finished goods determines their classification after completion. One manufacturer's finished goods inventory may be a retailer's merchandise inventory, dropshipping inventory, or another manufacturer's raw material or component. "Finished goods inventory", also known as "finished product inventory", is a term that can vary depending on the context. It’s also known as finished product inventory. They are the culmination of raw materials and items in every stage of production. Here’s what finished goods inventory is, how to calculate it, and why it's one of the best types of inventory out there.įinished goods are the final products that manufacturers sell to buyers, such as upstream vendors or retailers.
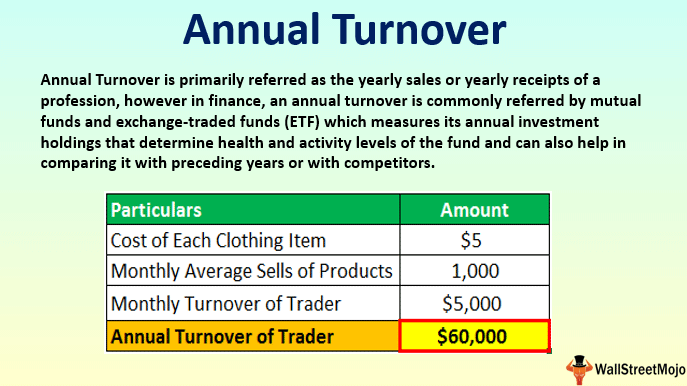
And they all improve when you invest in tightening up your finished goods inventory process and reporting (see what is inventory).
